
Therefore, the focus is on short arc improvement which led to another variable of short circuiting transfer mode called “modified short arc.” However, transfer mode located in the midvoltage output, such as pulse and spray, is also subject to development. The trends in developing regulation of metal transfer have been to reduce the heat input and spatter during molten deposition and increase arc stability. Basically, there are five transfer modes short circuiting mode, globular mode, spray mode, pulse mode, and rotating mode.
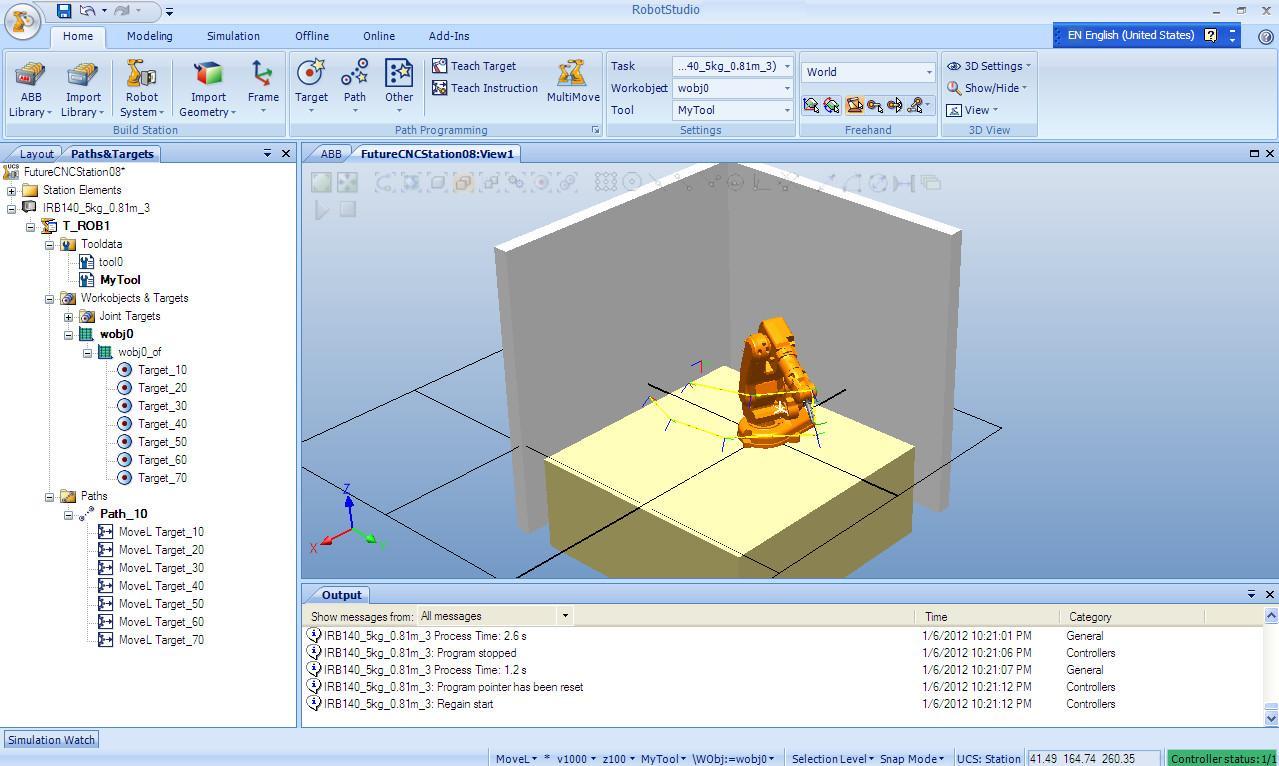
The mode of metal transfer depends on the material being welded and the productivity targeted. Secondly, metal transfer mode regulation as a result of power output regulation a mode of droplet transfer is obtained. Arc types and their working ranges, solid wire of 1.2 mm, shielding gas: argon-rich mixtures. This regulation involves the timing of the current and voltage, the transfer of the molten metal in the pool, the arc ignition, and the constancy of the arc control for the constant tip-to-work piece distance (CTWD) and shielding gas flow control.įigure 1.37. The regulation process is an important issue which aims to predict every single sequence of the arc welding process. In later 1990s, the waveform control welding process by digitalization become possible with the development of microprocessor and their availability in the open market. , the digitalization control of the sequence part became possible approximately at the same time of the appearance of the inverter-controlled powers sources.

However, the operating shortest time is limited to 0.01 s (100 Hz), even with the fastest wire feeder. This performance has reached the level of speed which enables a control of the behavior of the cathode electrode. The digitalization of the power source and the increase of the inverter’s control frequency circuit have contributed to increasing the output control of welding to frequencies of up to 100 Hz. Consequently, the value is the same prior to next operation if needed. The digital feedback control is more stable when it can lead to voltage fluctuation and other perturbation. In addition, this approach opens to digital feedback control rather than analog feedback control. This led to a rapid electronic control capability to control both the static and dynamic properties of the power source.
#ABB ROBOTSTUDIO 6.02 PLUS#
Schematic overview of the different types of the power source and the current or voltage regulation.īesides, an approach with AC line rectifier plus inverter was implemented in power source, the mains AC voltage is rectified, and transistors are used to produce a higher frequency in the range of 20-100 kHz.
#ABB ROBOTSTUDIO 6.02 MANUAL#
While manual welding may use any of the systems mentioned, push-pull systems are becoming the standard method of wire feeding in robotic applications because of the need for highly consistent feed speeds and defect- free arc starting.įigure 1.36. The control for feed speed may be mounted on the torch or on the wire feeder. They must also be able to reach the desired wire feed speed as rapidly as possible in order to give good and stable arc starting. The length of the umbilical cable is limited only by the voltage drop in the power delivery and return leads and perhaps the need to provide water cooling to the torch.Īll of these systems require that the wire is driven at a constant, controlled rate unaffected by continuous operation, variations in supply voltage or fluctuations in temperature. These rolls push the wire the short distance from the reel to the contact tip, enabling wires as small as 0.4 mm in diameter to be used. The final variation on this theme is the spool on gun torch which utilises a small 100 mm diameter wire reel mounted on the welding torch and a set of drive rolls in the torch body. This enables small diameter wires to be fed up to 15 m from the wire reel. The push–pull system is a combination of the above two systems with a set of drive rolls at both the wire reel feeder and in the torches illustrated in Fig. 7.11.
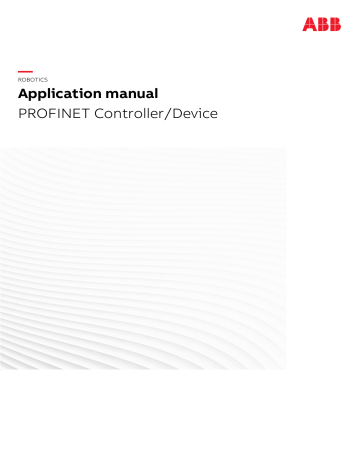
MIG torches equipped with ‘pull’ wire drive rolls.
